Exploring the Advantages of OEM CNC Turn Parts Factory
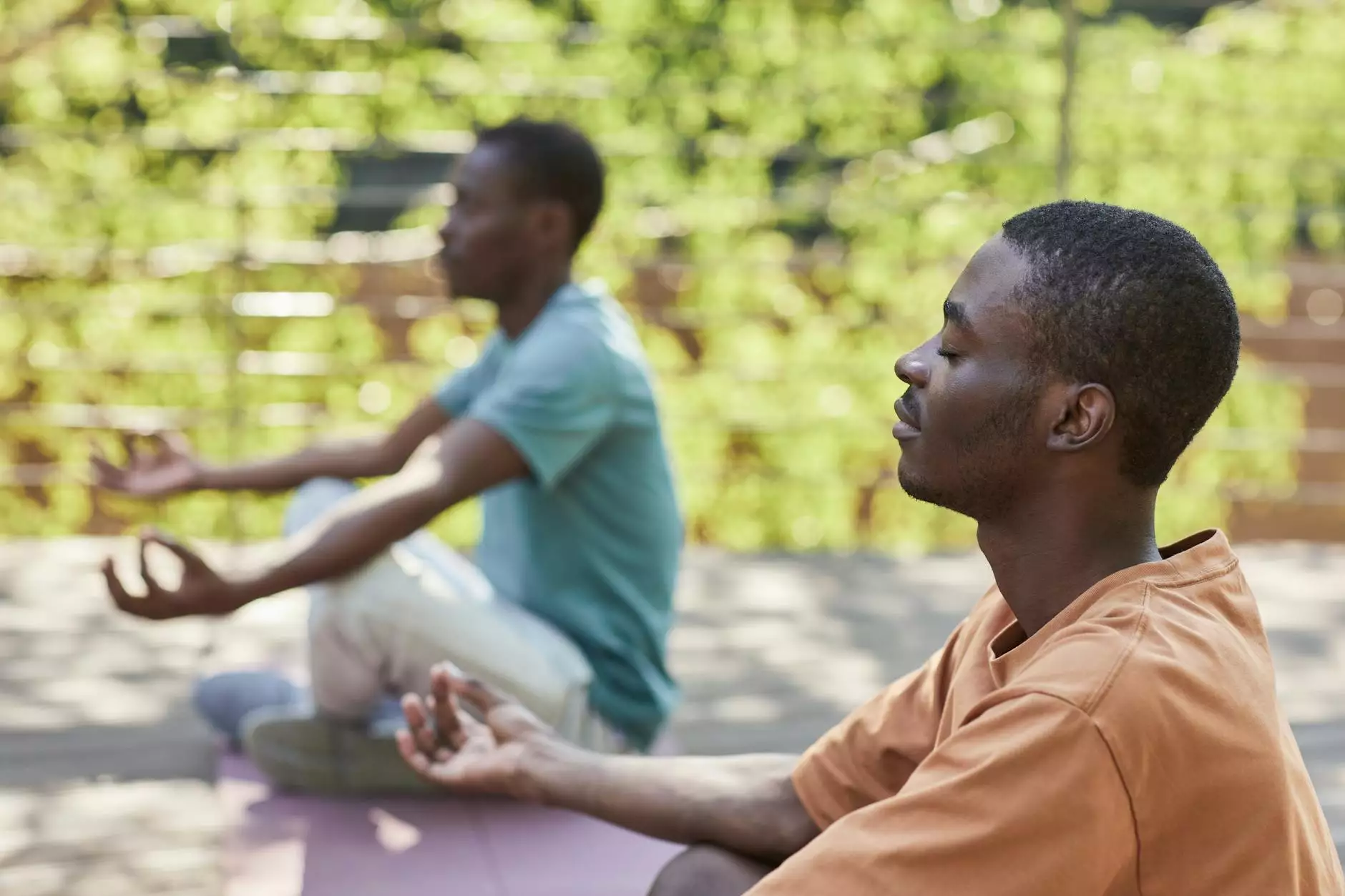
In the intricate world of manufacturing, the collaboration between various components is critical to achieving success. One of the leading forces in this arena is the OEM CNC turn parts factory. This facility specializes in the precision crafting of components essential for a wide range of industries, including automotive, aerospace, and consumer electronics. Through this article, we will delve deep into the numerous benefits offered by OEM CNC turning services and how they can substantially impact your business.
Understanding CNC Turning and Its Importance
CNC turning is a manufacturing process that utilizes Computer Numerical Control (CNC) machines to rotate a workpiece and cut it into the desired shape. The precise control offered by CNC technology allows for the production of intricate designs and high-quality components with minimal human intervention. The significance of an OEM CNC turn parts factory is underscored by its ability to produce:
- High Precision Components: Precision is paramount in manufacturing. CNC turning can produce parts with tolerances as tight as a few microns, ensuring that every piece meets strict specifications.
- Complex Designs: With advanced software and tooling, CNC turning can accommodate complex geometries that would be impossible to create with traditional machining methods.
- Consistency and Reproducibility: Once a design is programmed into the CNC machine, it can produce identical parts repeatedly without variances, crucial for mass production.
The Role of an OEM CNC Turn Parts Factory
Ultimately, an OEM CNC turn parts factory serves as a vital partner to various industries by providing not only the components they need but also expertise in manufacturing processes. Here are several ways these factories contribute to business success:
1. Cost Efficiency
By streamlining the production process, an OEM CNC turn parts factory can significantly reduce manufacturing costs.
- Reduced Waste: CNC turning minimizes material wastage through precise cutting techniques.
- Less Labor Intensive: Automation leads to lower labor costs, as fewer operators are needed to oversee production.
- Bulk Production Capabilities: These factories can handle large order volumes, achieving economies of scale that reduce per-unit costs.
2. Customization Options
Every business has unique requirements, and an OEM CNC turn parts factory excels in providing customized solutions. Their services include:
- Tailored Specifications: Clients can provide specifications for sizes, shapes, and materials to meet their specific needs.
- Prototyping Services: Many factories offer prototyping before full-scale production, allowing businesses to test and refine their designs.
- Material Variety: These factories often stock a wide range of materials—such as aluminum, brass, and stainless steel—enabling diverse applications.
3. Advanced Technology Deployment
The industry is continually evolving, and an OEM CNC turn parts factory usually invests in cutting-edge technology to enhance its manufacturing capabilities:
- Latest CNC Machinery: High-tech machines allow for quicker setup times and enhanced precision.
- Software Integration: Advanced software solutions help in designing and planning the production process to eliminate inefficiencies.
- Quality Control Systems: Many factories incorporate rigorous quality control measures, ensuring that every piece produced adheres to industry standards.
Quality Assurance in CNC Turning
Quality is non-negotiable in manufacturing, particularly for industries with high safety standards such as aerospace and automotive. An OEM CNC turn parts factory implements a series of strict quality control practices, which include:
- Regular Equipment Calibration: Ensuring that machines are regularly checked and calibrated to maintain accuracy.
- Inspection Protocols: Every produced batch is subject to rigorous inspection processes to identify any potential defects.
- ISO Certification: Many factories achieve certification from international quality standards organizations, proving their commitment to quality.
The Future of OEM CNC Turning Services
As technology rapidly advances, so too does the potential for OEM CNC turning. The future promises exciting developments, including:
- Artificial Intelligence Integration: AI technologies could enhance manufacturing processes, leading to smarter production methods and predictive maintenance.
- Sustainability Practices: Growing awareness of environmental concerns has led many factories to adopt sustainable practices, utilizing recyclable materials and cleaner production techniques.
- Increased Automation: The incorporation of robotics alongside CNC machinery will enhance production speeds while maintaining high quality.
Conclusion: Partnering with an OEM CNC Turn Parts Factory
In conclusion, collaborating with an OEM CNC turn parts factory stands as a strategic move for businesses aiming to enhance their manufacturing processes. The advantages—ranging from cost efficiency and customization to quality assurance and technological advancement—position these factories as pivotal partners in the manufacturing ecosystem. Whether you are in the automotive sector, aerospace industry, or any field requiring precision parts, choosing the right CNC turning partner can make all the difference in achieving your business goals.
At Deep Mould, we pride ourselves on being at the forefront of CNC turning technology, ready to meet your unique manufacturing needs. Our experienced team is committed to delivering high precision components tailored specifically to your requirements. Discover how we can help elevate your business by visiting deepmould.net.