Injection Molded Plastics: Revolutionizing Manufacturing and Design
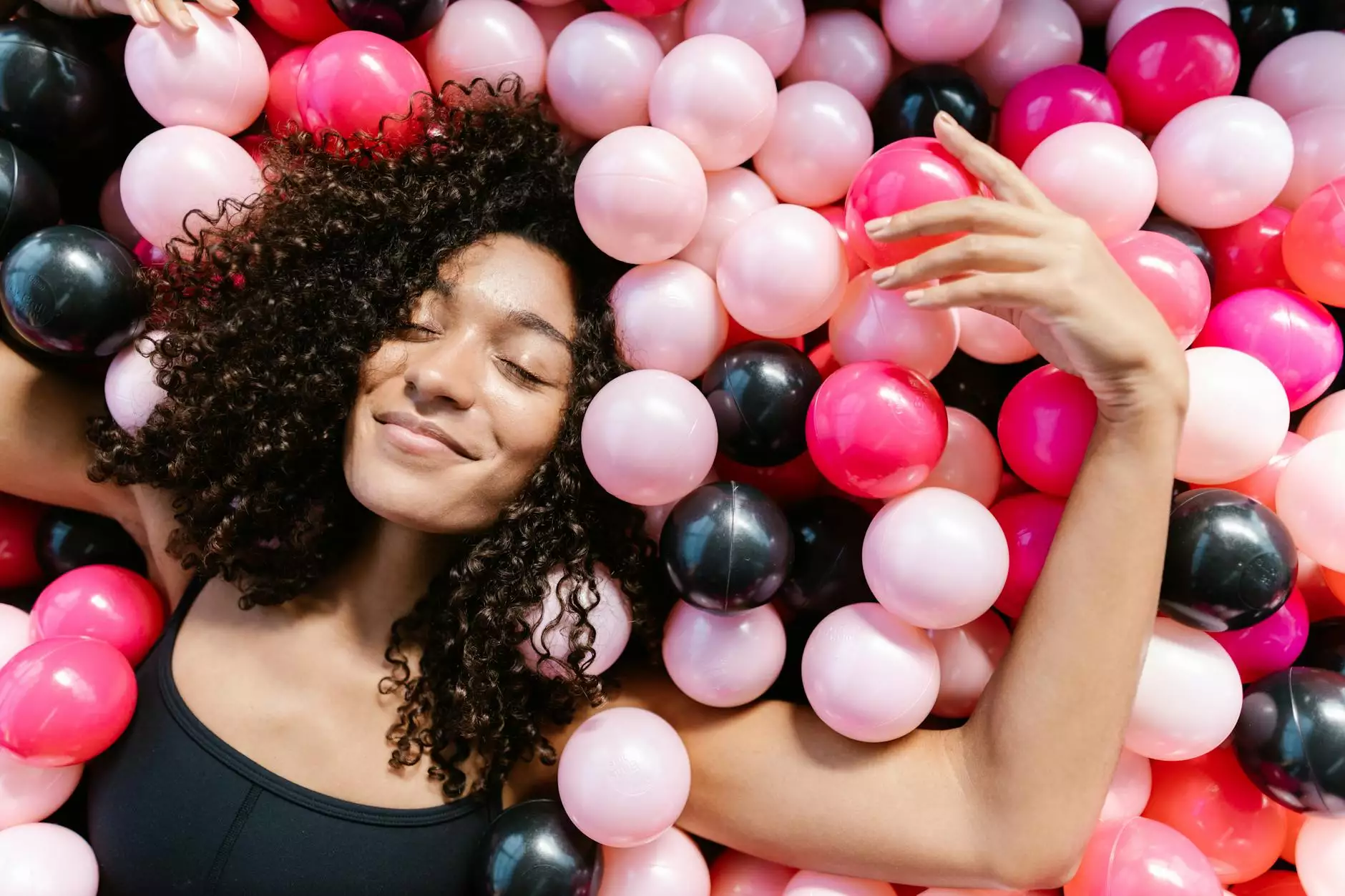
Injection molded plastics have become a cornerstone of modern manufacturing, providing innovative solutions across various industries. This article delves into the intricacies of injection molding, its applications, benefits, and why it's a game changer for manufacturers and designers alike.
The Basics of Injection Molding
Injection molding is a manufacturing process for producing parts by injecting molten material into a mold. The materials used can be either thermoplastic or thermosetting polymers. The process is widely used because it allows for high precision and mass production.
How Injection Molding Works
The injection molding process consists of several key steps:
- Clamping: The two halves of the mold are closed and clamped together.
- Injection: The molten plastic is injected into the mold cavity under high pressure.
- Cooling: The material cools and solidifies within the mold.
- Opening: The mold is opened, and the finished part is ejected.
Materials Used in Injection Molding
Injection molded plastics are created using a variety of materials, each with unique properties that cater to different applications:
- Thermoplastics: These materials can be heated and cooled repeatedly without losing their structure. Examples include ABS, Polypropylene, and Nylon.
- Thermosetting Plastics: Unlike thermoplastics, these materials undergo a chemical change when heated and cannot be remolded. Examples include Epoxy and Phenolic Resins.
Applications of Injection Molded Plastics
The versatility of injection molded plastics allows them to be used in numerous industries, including:
1. Automotive Industry
Injection molding is extensively used in the automotive sector for parts like dashboards, bumpers, and interior components. The process is favored for its ability to create complex shapes with high strength and lightweight characteristics, enhancing fuel efficiency.
2. Consumer Electronics
From smartphone casings to laptop components, injection molded plastics play a critical role in consumer electronics. The ability to produce intricate designs at scale meets the demand for aesthetically pleasing yet durable products.
3. Medical Devices
The medical industry relies on injection molding for manufacturing precision components like syringes, blood filters, and implantable devices. The stringent quality controls within the injection molding process ensure that these products are safe and effective.
4. Home Goods and Appliances
Kitchenware, storage containers, and small appliances are often made from injection molded plastics. This method allows for affordable mass production while maintaining high-quality standards.
5. Packaging Solutions
Injection molded plastics are also extensively used in packaging, providing airtight sealing and protection for products. They cater to food safety, pharmaceuticals, and consumer goods.
Benefits of Using Injection Molded Plastics
Investing in injection molded plastics offers several advantages:
- Cost Efficiency: Although the initial costs for mold creation can be high, the per-unit cost decreases significantly with large production runs, making it economical for high-volume manufacturing.
- Design Flexibility: Designers can create complex shapes that would be difficult or impossible to achieve with other methods. The ability to add varying textures and colors enhances product appeal.
- High Precision: Injection molding allows for fine tolerances, resulting in consistent quality and performance across production runs.
- Reduced Waste: The process generates minimal scrap material compared to traditional manufacturing methods, promoting sustainability.
- Shorter Lead Times: The speed at which injection molded plastics can be produced accelerates time-to-market for new products.
Considerations in Injection Mold Design
To maximize the benefits of injection molding, particular attention must be paid to the design of the mold:
1. Draft Angles
Including draft angles in the mold design enables easier part removal and reduces wear on the mold itself, extending its lifespan.
2. Wall Thickness
Consistent wall thickness is crucial to avoid warping and to ensure uniform cooling. Variations can compromise the strength and appearance of the final product.
3. Venting
Proper venting ensures that trapped air does not create defects during the injection process, maintaining a high-quality finish on the molded parts.
4. Cooling Channels
Incorporating cooling channels into the mold design optimizes the cooling phase, reducing cycle time and increasing production efficiency.
Future Trends in Injection Molded Plastics
The landscape of injection molded plastics is continually evolving, influenced by technological advancements and market demands:
1. Sustainability Initiatives
With increasing environmental awareness, the industry is shifting towards biodegradable and recyclable materials. Manufacturers are also focusing on reducing their carbon footprint during the injection molding process.
2. Automation and Industry 4.0
Integrating automation technologies into the injection molding process allows for greater efficiency, precision, and consistency. The advent of Industry 4.0 is paving the way for smart factories that leverage data to optimize production.
3. Advanced Materials
Research into new high-performance materials is expanding the capabilities of injection molding, allowing the production of parts that can withstand extreme conditions without compromising performance.
Choosing the Right Partner for Injection Molding
When selecting a provider for injection molded plastics, consider the following factors:
1. Experience and Expertise
Look for a company with extensive experience in injection molded plastics and a proven track record of successful projects in your industry.
2. Capability and Technology
Assess the technologies and equipment the supplier utilizes to ensure they can meet your specific production needs and quality standards.
3. Customer Support
A reliable partner should offer excellent customer support, assisting you through every phase of the project from design to delivery.
Conclusion
Injection molded plastics are undeniably an integral part of modern manufacturing, offering significant advantages in terms of efficiency, precision, and sustainability. As industries continue to evolve, embracing these innovative materials and processes is vital for staying competitive. For businesses looking for quality and expertise in injection molding, DeepMould.net stands as a trusted partner in achieving your production and design goals.